TJ-II:Construction: Difference between revisions
No edit summary |
m (→Vacuum vessel) |
||
Line 9: | Line 9: | ||
The vacuum vessel is made of non-magnetic steel (304 LN) with a thickness of 10 mm. | The vacuum vessel is made of non-magnetic steel (304 LN) with a thickness of 10 mm. | ||
The octants with flanges have been manufactured separately and were assembled in-situ by welding. This assembly was done directly around the central conductor CC/HX, already placed in position. The CC/HX coil is outside of the vaccuum vessel thanks to a helical groove built into the vessel. This groove has a wall thickness of 7 mm for clearance reasons. | The octants with flanges have been manufactured separately and were assembled in-situ by welding. This assembly was done directly around the central conductor CC/HX, already placed in position. The CC/HX coil is outside of the vaccuum vessel thanks to a helical groove built into the vessel. This groove has a wall thickness of 7 mm for clearance reasons. | ||
Its groove is protected along the entire toroidal circumference against damage due to the bean-shaped plasma by 3 mm stainless steel sheets for low and medium power operation and graphite tiles for high power operation. Furthermore, the vacuum vessel is protected on the areas where the neutral beams deposit a residual shine-through heat flux. The vacuum vessel | Its groove is protected along the entire toroidal circumference against damage due to the bean-shaped plasma by 3 mm stainless steel sheets for low and medium power operation and graphite tiles for high power operation. Furthermore, the vacuum vessel is protected on the areas where the neutral beams deposit a residual shine-through heat flux. The vacuum vessel is pumped through four symmetrically spaced bottom ports to a base pressure of 10<sup>-8</sup> mbar. Four identical and independent vacuum pumping subsystems are used. | ||
<ref>[http://dx.doi.org/10.1109/FUSION.1993.518387 J. Botija et al, '' Vacuum vessel, wall protection, pumping system and poloidallimiters of the Spanish stellarator TJ-II'', 15<sup>th</sup> IEEE/NPSS Symposium on Fusion Engineering '''1''' (1993) 529-532]</ref> | <ref>[http://dx.doi.org/10.1109/FUSION.1993.518387 J. Botija et al, '' Vacuum vessel, wall protection, pumping system and poloidallimiters of the Spanish stellarator TJ-II'', 15<sup>th</sup> IEEE/NPSS Symposium on Fusion Engineering '''1''' (1993) 529-532]</ref> | ||
Revision as of 12:49, 23 September 2009
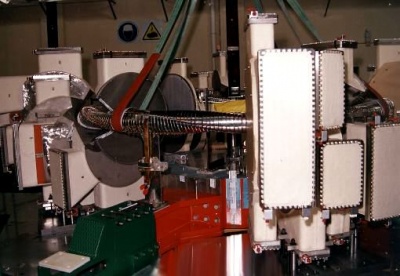
TJ-II is a highly flexible medium-size fusion device of the Heliac type constructed at CIEMAT between 1991 and 1997. The magnetic surface mapping was measured at low magnetic fields between December 1996 and January 1997, with excellent results. From January to September 1997 the commissioning of the device up to the design values was done, together with the assembly of the basic diagnostic equipment. [1] [2]
Vacuum vessel
The all-metal vacuum vessel of TJ-II has a helical geometry and has 96 ports. The vacuum vessel is made of non-magnetic steel (304 LN) with a thickness of 10 mm. The octants with flanges have been manufactured separately and were assembled in-situ by welding. This assembly was done directly around the central conductor CC/HX, already placed in position. The CC/HX coil is outside of the vaccuum vessel thanks to a helical groove built into the vessel. This groove has a wall thickness of 7 mm for clearance reasons. Its groove is protected along the entire toroidal circumference against damage due to the bean-shaped plasma by 3 mm stainless steel sheets for low and medium power operation and graphite tiles for high power operation. Furthermore, the vacuum vessel is protected on the areas where the neutral beams deposit a residual shine-through heat flux. The vacuum vessel is pumped through four symmetrically spaced bottom ports to a base pressure of 10-8 mbar. Four identical and independent vacuum pumping subsystems are used. [3]
Coil system
Seven water-cooled copper coil systems with maximum currents between 7 kA and 32.5 kA provide the helical confinement field. The Bitter-type toroidal coils are split in half for assembly reasons. Four sets of poloidal coils produce the vertical, radial and OH fields.
Precision machining and positioning
TJ-II is a very compact experimental device with highly stressed materials and very narrow tolerances to achieve good confinement properties. This required high quality standards for the fabrication and assembly of the device. For the high precision positioning of all stellarator components, a computer-based theodolite system was employed. A large number of tests were done during the assembly phase. Afterwards a comprehensive commissioning program was performed.
Power supply
The pulsed power supply was tested up to the maximum current values by means of a dummy load consisting of up to five inductively coupled coils. The distances between the coils were chosen in a way such that self and mutual inductances coincided with those of the coil systems of the stellarator, thus forming an electromagnetic image of TJ-II.
References
- ↑ M. Blaumoser et al, Construction, commissioning and first results of the Spanish Stellarator TJ-II, Fusion Engineering, Proc. 17th IEEE/NPSS Symposium 1 (1997) 257 - 260
- ↑ C. Alejaldre et al, TJ-II assembly completed, Stellarator news 48 (1996) 1
- ↑ J. Botija et al, Vacuum vessel, wall protection, pumping system and poloidallimiters of the Spanish stellarator TJ-II, 15th IEEE/NPSS Symposium on Fusion Engineering 1 (1993) 529-532